50% of crane failure or total collapse is from improper use of outriggers. A proactive safety approach is to use outrigger pads on all setups. The outrigger pads will displace & reduce the PSI the ground “ sees ” from the point of contact of the outrigger/ shoe/ float/ pontoon on the equipment. The outrigger pads will also remind the personnel at the job site to ensure the outrigger system is being used correctly. Bigfoot is the first company to manufacture safety orange. This was done to address tripping hazards & make sure the outrigger system is deployed by bringing attention to the operator & other personnel on the job site.
The outrigger system shall be used according to the manufacturer’s standards.
- The setup & leveling is critical on any setup or with any style of outrigger system on the equipment. Always follow the manufacturer’s chart on level & grade % allowable for equipment to be set up.
- Get recent soil conditions. Getting a known ground bearing capacity ( GBC) will help with knowing what outrigger pad is the best fit.
- Check for location & know where utilities are overhead & underground.
- Maintain proper clearances on overhead power lines.
- Outrigger pads shall not be used to bridge any gaps or span over voids.
After the equipment is set up, level & according to the manufacturer recommendations & with Bigfoot outrigger pads, perform a dry run with spotters. The boom should be run over & around all the outriggers with a spotter not under the boom but looking at the outriggers. The spotter is looking to see if any of the floats are sinking, shifting, or sliding. If there is any issue, stop & stow the boom. Now is the time to re-check the equipment level, improve soil conditions or add Bigfoot outrigger pads & cribbing. There are some great starting points with setting up, but this will not cover all equipment set up. Having a lift director or person in charge on the job site to address setting up will help to avoid crane failure.
- Knowing the max PSI/ PSF ( this does not factor in shock or impact loading, which is common in DEMO & tree care or removal work. Speed plus mass equals force, which is measured in PSI/PSF & will go through the outrigger system).
- Size of outrigger/ shoe/ float/ pontoon on equipment
- Soil conditions
In many but not all setups, having this information will address the 3 times the square surface area on grade A soil conditions. The 3 times the square surface area on grade A soil conditions will displace the PSI from the equipment through the outrigger pad, depending on the GBC value that needs to be maintained. If there is a known GBC value needed & an engineer has values needing to be reached, Bigfoot can help.
Crane Failure
Cribbing or dunnage should not meet or exceed the height of the base outrigger pad. Example: A 36 X 36 at 2” ( P363620 ) should not have cribbing or dunnage meet or exceed 36” on any setup. The bottom layer or base outrigger pad will be carrying the PSI ( when you see pictures of other outrigger pads with wood cribbing or dunnage underneath or on bottom, the cribbing or dunnage is carrying the load, the top pad is the cushion). Knowing this, the sheer value is needed on the setup as well. Bigfoot recommends using the same material to maintain consistency with sheer values, our custom composite cribbing is made from the same material as our outrigger pads.
Bigfoot’s American custom composite has no grain lines. This allows the set up of outrigger pads & cribbing to be exceptionally user-friendly. This will eliminate the question of vertical pressure or out & down outrigger systems, which direction should the pads or cribbing face? The sheer value of Bigfoot’s custom composite is the same in either direction. Bigfoot’s material is not injected or extruded or 100% recycled material, these materials will have different directional shear values & need to be addressed in addition to setups. This is another area that Bigfoot has & can help with operators, lift directors, or personnel in charge. This will without question, using Bigfoot outrigger pads, help with setups & reduce human error to make sure the hard-working personnel are using STRENGTH/ STABILITY/ SAFETY on their job sites & equipment.
Safe Equipment Setup with Proper Cribbing and Blocking
Your SAFETY is our utmost concern at Bigfoot. We are dedicated to providing you with essential information you need to ensure the safe operation of cranes and heavy equipment across various ground surfaces. Employing appropriate cribbing and blocking techniques is pivotal in this process.
The Significance of Cribbing and Blocking
Cribbing establishes the sturdy foundation for elevating outriggers and stabilizers to greater heights, while blocking is instrumental in the even distribution of weight for heavy loads. These methods are integral to protecting operators from potential harm and guiding you in selecting the most suitable approach for supporting your equipment.
Key Definitions
- Ground Conditions: This term pertains to the ground’s capability to withstand the weight of the equipment.
- Support Materials: This encompasses materials like blocking, mats, cribbing, or similar devices used to provide support.
Choosing the Appropriate Materials
When selecting materials for cribbing and blocking, consider the following:
- Make sure that the selected material can withstand the heavy loads exerted by the outrigger.
- Do not use materials exhibiting cracks, deformations, rot, bending, wear, or damage.
- Use materials larger than the outrigger’s foot.
- Choose materials with ample thickness, width, and length to prevent load shifting, tipping, or excessive settling.
- Keep materials free from oil, grease, and debris, and keep them dry to prevent slipping.
Safe Usage of Cribbing and Blocking
For secure utilization, please adhere to the following guidelines:
- Personnel should wear steel-toed boots, gloves, and eye protection when handling cribbing and blocking.
- Place materials on a solid, level base or foundation to ensure uniform weight distribution.
- Verify that no debris is beneath the cribbing or blocking, obstructing proper ground contact.
- Position the cribbing directly beneath the outrigger and stack it to prevent slippage.
- Regularly inspect cribbing and blocking during equipment operation for any indications of settling, slippage, cracking, bending, crushing, or shear failure.
- The cribbing should never exceed twice the width of the blocking base.
Determining the Correct Blocking Size
To ascertain the suitable size for cribbing or blocking, consider the following rules:
- Rule of 5: Divide the unit’s maximum lifting capacity (in tons), e.g., 50 tons, by 5. This yields a requirement of 10 sq. ft. of cribbing or blocking.
- Rule of 3: Multiply the square footage of the crane’s floats by 3. For instance, a 2×2 float equals 4 sq. ft. Multiply 4 sq. ft. by 3, resulting in a requirement of 12 sq. ft. of cribbing or blocking.
For more comprehensive guidance, we encourage you to consult OSHA’s standard on cranes and derricks in construction (1926 Subpart CC). Your safety remains our top priority, and we are here to support you in the safe utilization of your equipment.
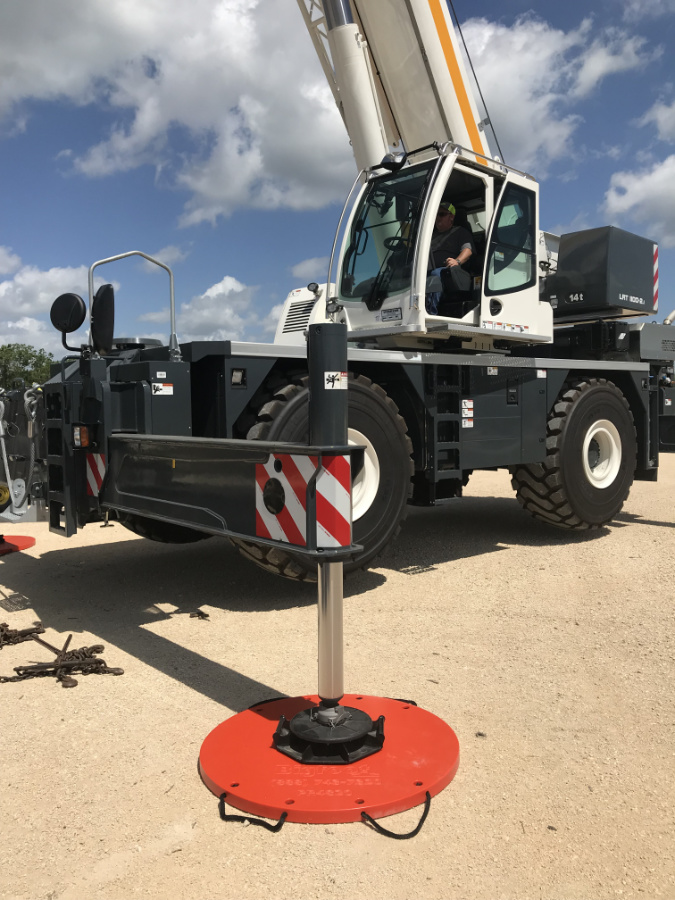
Ground Bearing Capacities of Various Soil Types
Soil Type | (G.B.C.) |
---|---|
Virgin Ground | 22 PSI |
Asphalt | 29 PSI |
Compressed crushed stone | 36 PSI |
Clay/Silt soil, firm | 43 PSI |
Mixed granular soil | 51 PSI |
Firm compacted gravel | 58 PSI |
Firm compacted gravel (more compacted) | 72 PSI |
Firm compacted gravel (more compacted, class 5) | 109 PSI |
Brittle weathered rock | 145 PSI |
Concrete (unknown mix) | 1000 PSI |
Type A Soil
Type A soil has a compressive strength of at least 1.5 tons per square foot. It is not fissured nor does it have water seeping through it. It should not vibrate from pile drivers or heavy traffic
Type B
Type B soil does not stick together as much as Type A soil. Its compressive strength is between 0.5 and 1.5 tons per square foot.
Type C
Type C soil is very unstable because its particles don’t stick together and it has a low compressive strength equal or less than 0.5 tons per square foot. Any soil with water seeping through it is classified as Type C.
Ground Bearing Capacity
with Outrigger Pad
Weight: 35,000 lbs
Float: 12″ x 12″ = 144 in2
Pad: 36″ x 36″ x 1.5″ = 1,296 in2
Bigfoot outrigger pad broadcasting PFS
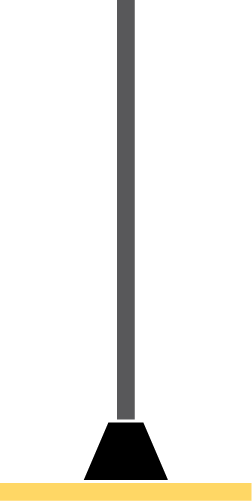
Mixed Granular Soil
GBC: 51psi / 7,344 psf

3,888.88 psf
3,888.88 psf < 7,344 psf
PSF no longer meets or exceeds allowable
Ground Bearing Capacity.
Disclaimer These schematics and figures do not include the more complex structural/civil/geotechnical engineering calculations required for an official lift plan. This example is meant to illustrate the basics of weight broadcasting required to stay underneath the ground bearing capacity limit.